Unique Embroidery Design for Anime Fan Apparel
Unique Embroidery Design for Anime Fan Apparel is part of our unique collection of anime embroidery designs! Perfect for personalizing apparel, bags, home decor, and accessories, these high-quality patterns feature iconic characters and scenes from popular anime series. Compatible with most embroidery machines, each design is detailed with precision and vibrantly colored, capturing the essence of anime art. Whether you’re stitching for another anime fan or adding your favorite characters to your personal collection, our anime embroidery designs are ideal for showcasing your passion. Bring your favorite anime moments to life and give your projects a bold, creative touch with these eye-catching designs!
Product Details
- Format: Instant Digital Download
- File Types: PES, DST, EXP, VP3, JEF, HUS
- Sizes: Available in 4″, 5″, and 7″
- Resolution: High-quality stitch files compatible with various embroidery machines
Key Features
- Personalization: Ideal for apparel, accessories, and home decor
- High Quality: Optimized stitch files for smooth lines and precise details
- Multiple Sizes: Choose the perfect size for your project
- Ease of Use: Ready-to-download files compatible with most embroidery software
Why Choose Our Designs on Embrodesign.com?
- Premium Quality: Crisp, detailed embroidery designs for professional results
- Instant Access: Download your files immediately after purchase
How to Use
- Purchase and download the embroidery files instantly
- Import the files into your embroidery software
- Stitch the designs onto shirts, bags, and more
Download now on Embrodesign.com and start creating beautiful embroidery projects today.
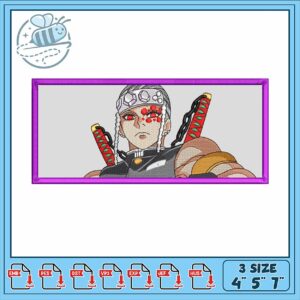
Reviews
There are no reviews yet.